Housing has recently become a crisis issue for many Canadians, but Indigenous communities have been tackling a lack of quality housing for decades. Now, Wahkohtowin Development is proposing a solution for First Nations in Northern Ontario.
One Bowl is a social enterprise with a “tree-to-home” solution focusing on the full cycle of the housing supply chain.
“We fired up a not-for-profit to actually partner with the private sector to develop thermal technology to create culturally appropriate homes,” said David Flood, general manager for Wahkohtowin Development and an Indigenous registered professional forester.
Working with Boréal Products, One Bowl is expediting the manufacture, construction and delivery of modular homes designed to meet Indigenous housing needs while also creating economic opportunities for participating communities.
Based in Chapleau Cree First Nation, One Bowl is a fully Indigenous-owned not-for-profit, led by Wahkohtowin, a collaborative initiative composed of three First Nations in the Northeast Superior area: Chapleau Cree First Nation, Missanabie Cree First Nation, and Brunswick House First Nation.
The organization incorporated in 2022 with one employee, Candace Larsen, in the role of business development manager, after recognizing the need for quality, long-lasting housing for Indigenous communities.
“A lot of Indigenous communities were in homes that were cracking, shifting, warping, and ended up being condemned in about seven years,” said Larsen.
Building homes in Northern Ontario First Nation communities often meant transporting a house in sections. Builders would send four sections of a house to a community and a construction team would follow, assemble it, and then leave.
“No Indigenous organization was contracted to build or to outfit it, and no capacity internally from the community was utilized to build the home,” Larsen said.
“So everybody in that community got to watch external workers come in, make money and profit off of this home, and then leave.”
The difference with One Bowl is that it involves the communities. It allows for entrepreneurial development for residents, from learning trades, like drywalling, to purchasing tools and fixtures in their community hardware stores.
Boréal Products, based in Alma, Que., is providing their Thermologs for the housing. The Thermolog is made from four dried white pine planks that are used as interior and exterior siding, with high-density expanded polystyrene in the centre to provide the necessary insulation.
Themalogs are rated for R30 in walls and up to R70 for roofs, which exceed industry standards for modular housing.
Like assembling a log home, the Thermologs are stacked to construct the shell of the house. A foundation, if wanted, plumbing, electrical, and interior walls all have to be added.
“You can construct an 1,800-square-foot home in 12 days with eight unskilled individuals,” Larsen said.
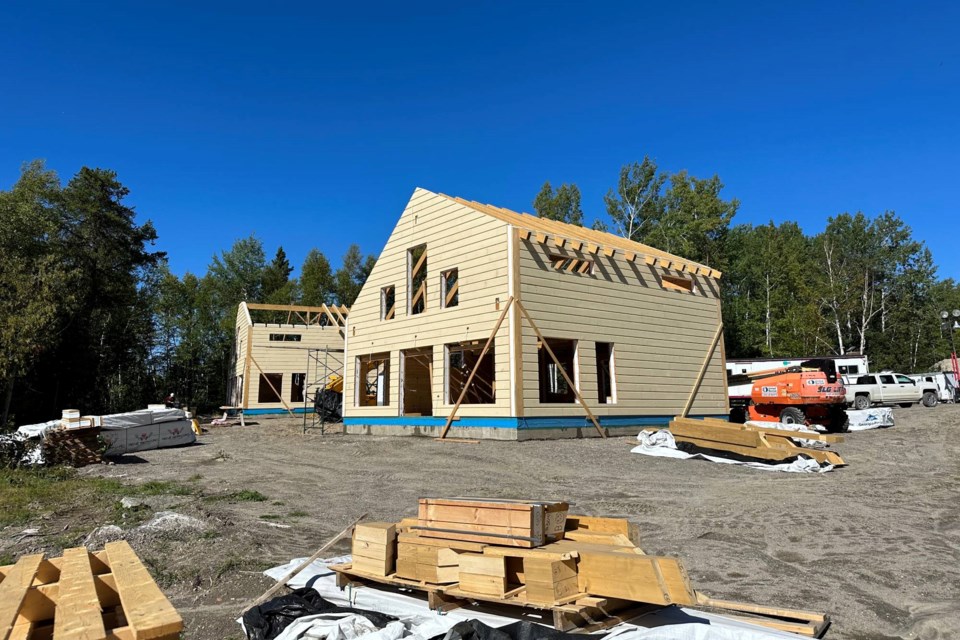
As the designated distributor of Boréal Products for First Nations in Northern Ontario, One Bowl provides the engineered plans for the different models, which include three-bedroom and two-bedroom homes, with an engineer stamp indicating it meets code.
A housing kit runs for about $75,000 for a 26-foot by 28-foot shell. Brunswick House First Nation has purchased four kits and has constructed all four at the same time. One Bowl has more kits going further north to Fort Albany and Kasheshwan.
The organization’s ultimate goal is to have full stewardship over the entire supply chain.
One Bowl is currently seeking funding that would enable it to purchase a majority ownership in a Thermolog manufacturing facility, to be established in Sturgeon Falls, west of North Bay, Larsen said. Once complete, the facility would have the capacity to supply over 500 homes annually to the Ontario market.
Revenue generated through that partnership, along with other limited partnerships, will be reinvested back into the program for housing services and supports, training programs, and mobile utility trailers.
Larsen said One Bowl sees this as a long-term strategy to stop economic leakage, provide employment, and own the entire process.
Ultimately, the hope is that this will lead to lower costs per unit for member nations and ease the way for Indigenous home ownership.
“They’re really having to break down probably 10 more barriers to the one that a non-Indigenous organization is going to have to deal with,” Larsen said.
“But with a full cycle housing supply chain transformation like this in place, we’re able to focus on each stage and bolster it.”
To help communities learn more about the process and opportunities, One Bowl will be holding an Indigenous Housing Symposium June 24-26, 2024 in Chapleau. Participants will have the opportunity to take part in a build and tour homes already built.
Larsen said One Bowl realizes it has a solution that would benefit many First Nations and the organization is currently expanding its board of directors.
“We’re not limited to servicing one specific region, (although) we are currently servicing more so around Chapleau,” Larsen said.
“But that’s because those are the three nations that came forward and said, ‘We need this and we need to be a part of this.’
“We’re in talks with people in British Columbia, Nova Scotia, and PEI.”